Intel Corp., the world's biggest chip maker, is unique in the way it rolls
out new manufacturing methods, perfecting it in a laboratory and then
painstakingly duplicating it at factories around the world.
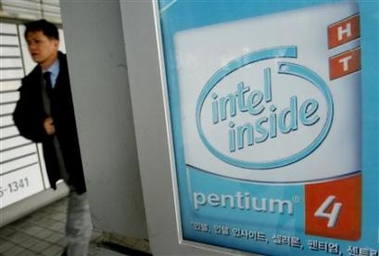 A man walks past an
advertisement board for Intel'in this Feburary 10, 2006 file photo. Intel
Corp., the world's largest chip maker, said on Tuesday it would spearhead
an initiative to sell cheaper computers in India to increase usage and
desktop penetration in Asia's third-largest economy.
[Reuters] |
The strategy, first employed in the mid-1980s, is called "Copy Exactly." And
the Santa Clara, California-based company means it.
Engineers strive to duplicate even the subtlest of manufacturing variables,
from the color of a worker's gloves to the type of fluorescent lights in the
building. Employees from around the world spend more than a year at a
development lab in Oregon learning their small piece of the new recipe so they
can bring it back to their home factory.
The idea, says Dave Aires, plant manager for Intel's Fab 12 factory in
Chandler, Ariz., is to capture the infinite number of intangibles that have
allowed a process to succeed in plants that have already brought it online.
"It's not just there's a specification or a recipe or a program you put into
a machine," he says. "It also is what the human being does and how they interact
with the machine."
Copy Exactly was implemented under the watch of Intel's current chairman,
Craig Barrett. In the mid-1980s, as Japanese companies began flooding the market
with high-quality memory chips that cost less than Intel's, Barrett was brought
in to make the factories more efficient.
One of the biggest contributions from Barrett, then Intel's No. 2 executive
under Andy Grove, was Copy Exactly.
"It turned us from what I would call an also-ran manufacturer to a pretty
good manufacturer," Barrett says.
The extremes to which Intel engineers go to control the precise conditions in
its dozen or so factories has become legendary.
About 10 years ago, Tom Franz, now an Intel vice president in charge of
manufacturing, was trying to figure out why one plant in Arizona wasn't hitting
the benchmarks achieved at another in Oregon, where the recipe was first cooked
up.
Then it hit him: Arizona's desert air was so much drier than the air in
Portland, and the engineers in Chandler were skipping several steps taken in
Oregon to dehumidify.
Intel scientists theorized that the dehumidifying, besides removing water,
also eliminated impurities such as ammonia. So engineers began adding water
vapor to the Chandler air, essentially making Portland air, and then subjected
it to the same dehumidifiers used in Oregon.
"It shows the level of things you've got to worry about when you try to make
something as complex as the chips we make," Franz says.
Under Copy Exactly, researchers spend more than four years perfecting a new
manufacturing technique in one of Intel's development factories in Hillsboro,
Ore. Once they are satisfied with the results, they work to meticulously import
every last detail to half a dozen or so chip factories around the world.
The technique contrasts with those at other chip makers, which tend to have
only one or two factories. At Advanced Micro Devices Inc., for instance, a new
manufacturing process is developed in a small portion of a factory and, once it
is perfected, it is rolled out to the rest of the plant.
Richard Doherty, research director at the Envisioneering Group, says the
technique is rooted in Intel's corporate culture and there's no scientific
evidence that it gives the company an edge.
"Other companies snicker a little bit at Intel going to such lengths to copy
exactly," he says.
But VLSI Research analyst Dan Hutcheson says there's a good reason for the
company's fixation with details such as the color and maker of paint in its
fabs. Paints, like many other objects, can emit contaminants that alter the
manufacturing process, Hutcheson says.
"All Intel cares about is that a chip comes out and is electronically the
same as every other chip coming out."