Auto marques forging ahead with die-cast bodies
By LI FUSHENG | CHINA DAILY | Updated: 2023-05-08 09:18
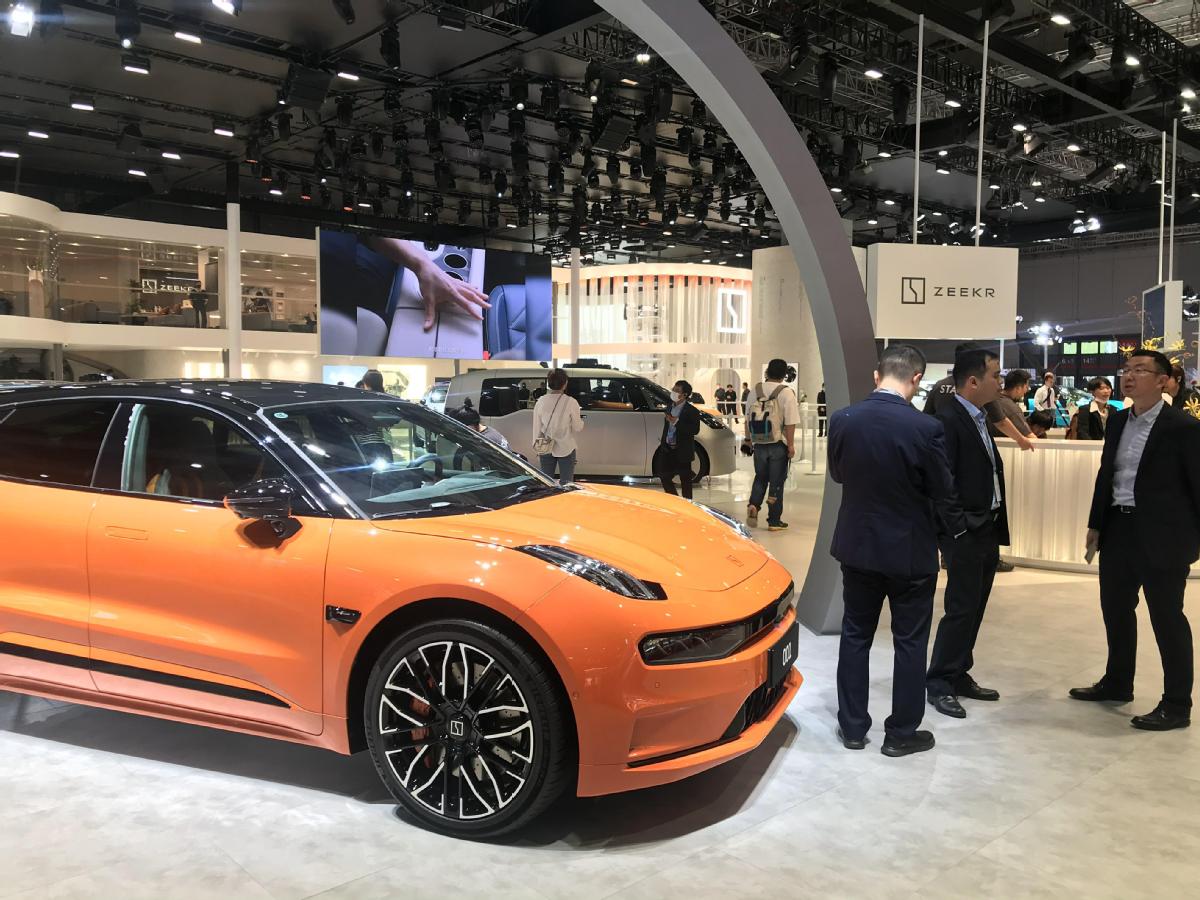
Electric vehicles have brought onboard features rarely seen in gasoline vehicles and now manufacturers are turning to innovations in the vehicle production process.
A growing list of marques are adopting the gigapress die-casting technique pioneered by Tesla to slash the cost of production.
Compared with the traditional method of car making, the technique has eliminated almost 800 welding points, cut defects, made the car lighter and boosted structural stiffness, said Zeekr.
The premium electric marque under Chinese carmaker Geely told Reuters that it has started using massive aluminum die-casts in its Zeekr 009, a six-seat MPV, that went on sale in November 2022.
Zeekr said it started looking into the technology in 2020 and purchased its giant presses from Hong Kong-listed LK Group.
The machines Zeekr uses have a pressing power of 7,200 metric tons. They help pump out underbody sections that each measure 1.4 meters long and 1.6 m wide.
The use of the heavy casting machines has helped simplify manufacturing and cut costs by up to 40 percent in some areas, according to Riccardo Ferrario, general manager of IDRA, owned by LK Group.
General Motors, the largest carmaker in the United States, is turning to large die-casting technology, which was used to help design its Cadillac Celestiq electric sedan.
Individuals close to Toyota have told Reuters the Japanese automaker is considering the possibility of deploying a version of the giga-casting technology to produce EVs.
Volvo, a Swedish carmaker owned by Geely, announced a plan in 2022 to invest in new EV manufacturing know-how, including "mega-casting" at its assembly plant in Torslanda, Sweden.
One risk in using giga-casting is the so-called repairability of vehicles. With body sections cast into single pieces, it could make them harder to repair if damaged in an accident.
With most cars made the traditional way, it might call only for the replacement of a fender or a bumper.
In the case of a giga-cast vehicle, however, that could possibly entail a replacement of the car's entire front or rear section, which increases the cost of repair for car owners.
Because of those concerns, some established companies, such as GM, are looking to use what engineers describe as smaller-scale giga-castings. These have cost and design flexibility advantages in low-volume applications.
Similarly, Toyota has begun looking at the possibility of turning to what some company insiders call "small portions" giga-casting technology that divides vehicle bodies into smaller castings, a Toyota source told Reuters.
The strategy is to address not only concerns about vehicle repairability but to cope with a wider range of vehicles in size and shape that Toyota sells globally, the person said.
To cope with repairs, Zeekr will be able to change select parts of the larger die-cast section in the event of a collision, rather than having to replace the whole thing.
"That should help reduce the repair cost after an accident," said Zeekr's manufacturing technology chief Jiang Kehong. "We believe customers should not pay extra for our technology innovation."